RESTORING “CAID”, A CLASSIC SWAN 431-12 FROM 1977
Ilmari Hentunen describes the progress of the work he and his wife, Karolina, have carried out on CAID
Finally, she was at home in Finland. We had already enjoyed sailing with her for two seasons in the Adriatic. While CAID is a well-founded and maintained yacht there is still a lot to do, so where should we start?
My wife’s opinion was to keep it as original as we could, which I happily accepted. There’s no point in ruining a perfectly decent yacht with disfiguring installations not belonging to the era or style the yacht is representing. However, in turn, there are some modern comforts we cannot live without when staying afloat longer than just some weeks.
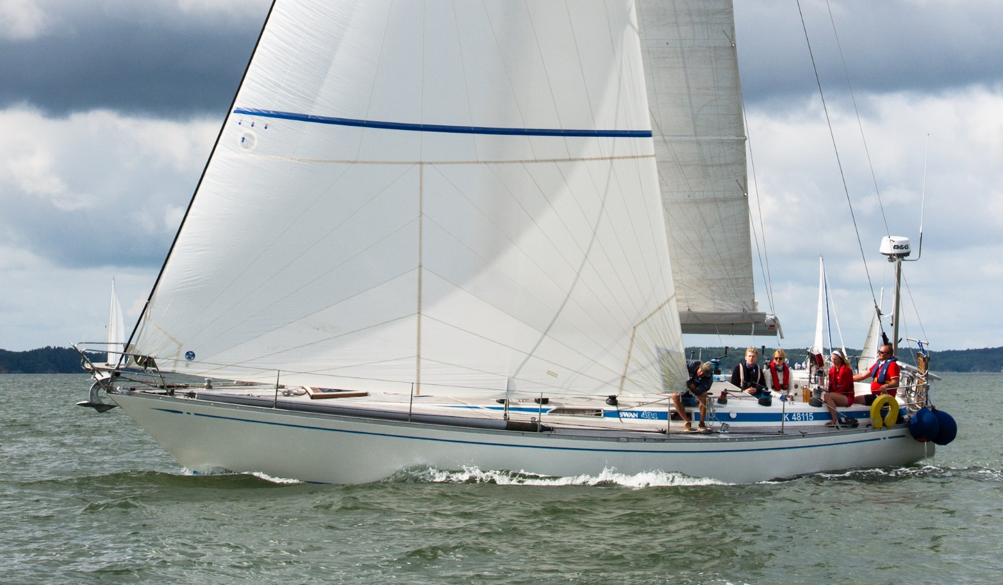
Full sail up (Photo: James Robinson Taylor)
2011-2013
We bought CAID near Venice in Italy in November 2011 after I had surveyed it carefully. Without the accumulated knowledge found on ClassicSwan.org, self-surveying would not have been possible as classic Swans are completely different beasts from those more usual average white boats. Obviously, we also had some luck as no major problems were found during the following years either. Naturally, CAID is not our first yacht so we were well prepared for this almost endless project of keeping her up.
During the two years in Italy, we changed some deck hardware to more modern solutions, replaced old electronics and refurbished the yacht as much as possible there. The spring preparations needed some careful planning before pointing the car’s nose to the south, as the whole of Europe lies between us and the yacht.
2014-2016
After sailing her back to our home waters we started working with her more intensively. During the winter weekends and evenings in 2013, we ripped out every part from the yacht which could be done without breaking it. This included all the floorboards, ceiling panels, salon table, cabin doors, all the other removable wooden parts, deck cleats and hatches, winches, and so on. Soon the hobby room of our apartment was full of wooden parts in mixed piles. After washing and drying them, we carefully sanded them to the bare teak. Some small defects were fixed invisibly with mixed epoxy and teak/birch dust as together this mix gave the best color match. Then they were ready for the varnishing. After 6 to 12 layers of two-component varnish sprayed or brushed on, the wooden parts looked almost as good as new. We were very pleased with the result, CAID was slowly approaching the level we’d like a Swan to achieve.
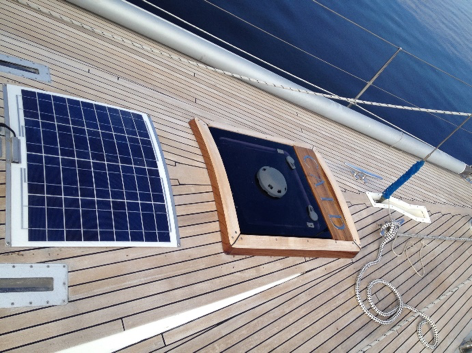
New deck hatch
During the spring we did all the wooden parts in the main salon and toilet. The fo’c’sle and aft cabin did not need any urgent attention so they were saved for a later time. New cushions were ordered in very light white colored HQ covers to lighten up the main cabin. All the deck hatches were replaced as their anodization was a bit dull after weathering so many years outside. I carefully measured all the deck curvatures and managed to build a new more flush deck hatch replacing the old sliding one. Thermal shrinkage due to climate differences between Italy and Finland had caused it to become too heavy to operate smoothly. But as it had been renewed lately and was in great condition, it found a new home on the deck of another classic Swan. We also replaced all the worn teak cleats with stainless steel ones of similar design. Some of the winches were replaced with self-tailing ones.
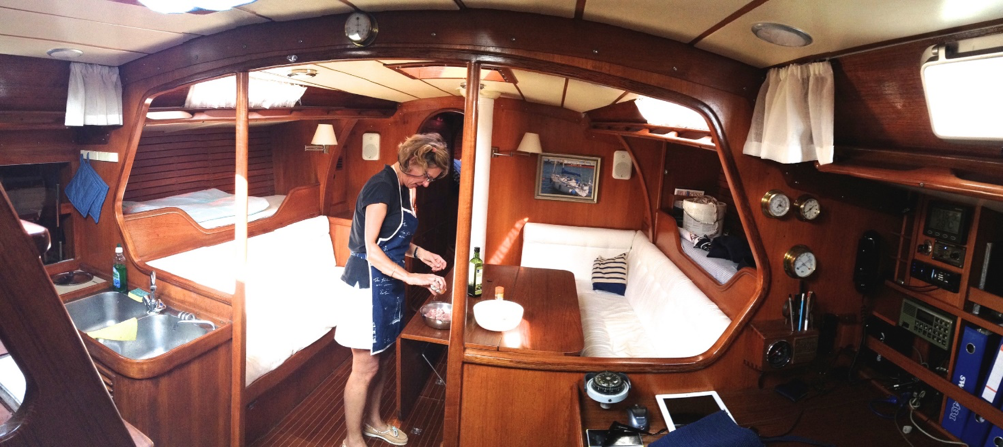
Refurbished main salon
From the electrical point of view, we decided to replace all the previous, not so old, navigation systems with new n2k items and ended buying the whole set of B&G components: nearly ten pieces of Triton MFD: s, double chart plotters, Wi-Fi, autopilot, ultrasonic wind transducer, AIS-B, etc. I also designed and installed an Ethernet network with internet connection (either with a cell phone as a bridge or a Bullet Titanium radio working as a Wi-Fi repeater) and also connecting the chart plotters to the new 4G radar through it. Kind of a base for a future IOT-solution (IOT = Internet of Things) also if needed.
For the increased power requirements, a Victron 120A/3500VA mains charger/inverter was installed under the double bunk in the after cabin and a new max sized Balmar alternator was bolted to the engine. It is adjusted with a clever voltage regulator by Sterling and matched carefully to the Trojan batteries, as is the case with the Victron charger too. Bendable solar panels of some 200 to 400W were also installed on the deck and other places with Victron MPPT controllers. The new big Victron charger/inverter was needed as it would be able to start the new A/C system, with or without the shore power connected. During the start-up, our A/C system will need more current than a typical shore power mains outlet will deliver but after starting we’ll be able to continue using it either with shore power or with the Yachts mains generator. I squeezed in as many deep cycle Trojan batteries as I could to their proposed place, but managed to get only 400AH together for house usage. Enough for our Baltic cruising purposes but more AHs are needed for our planned extended voyages. But there’s still room left under the bunks for some extension in battery capacity.
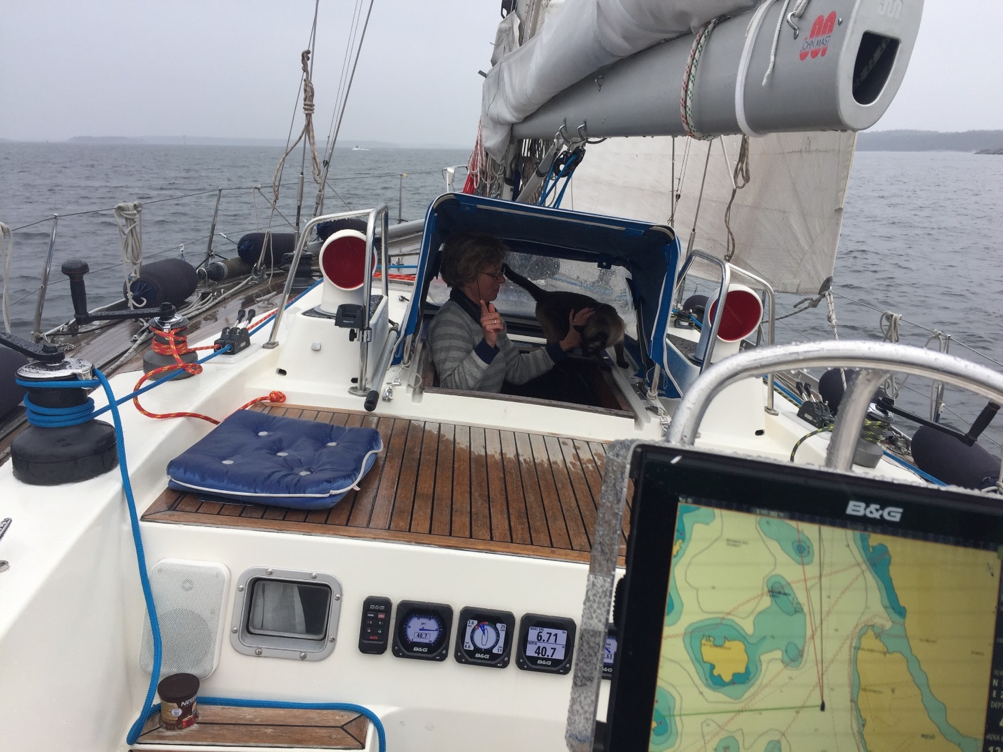
Midsummer in Finland 2016: raining and +12 degrees Celsius. Guess who’s helming the Yacht and who are enjoying the benefits of a dependable heater. The summer began a week later.
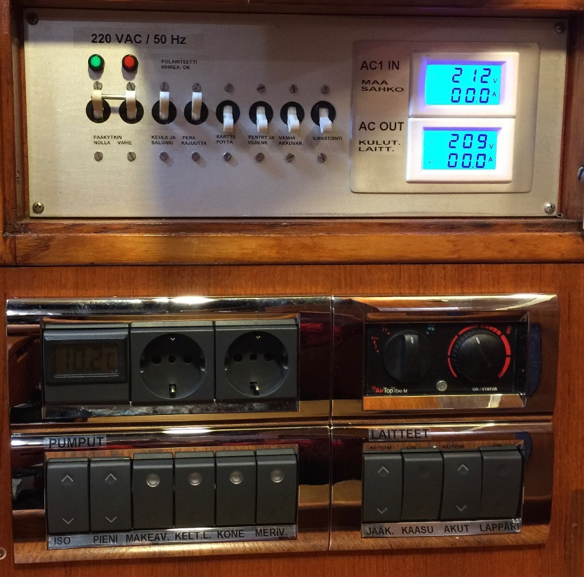
One of the new additional switch panels below a bit modified original one (AC). From the upper left: Freezer temp, AC-outlets, Webasto. The second row: 6xPumps, Freezer, LPG solenoid, Alternator Field control, Laptop 19V DC outlet.
A new Webasto 5.5kW heater with its dedicated 80-litre fuel tank was also installed to minimize the expected displeasure of our colder climate here. Luckily the co-skipper is in a good shape and those faraway corners during the installations were easily reachable for her, me being too well fed to do anything useful there. As we had so many new electrical items on board, I had to redesign all the switching panel solutions and install some twenty new switches. For example, we only had two electrical pumps before and now we have 9 different ones installed! A simple switch labeled “The Pumps” would not be sufficient on the electrical panel. The Swan quality was clearly shown when disassembling the electrical panel; all the labeled wires, switches, connectors, etc. looked and functioned still like new. And most of them were installed nearly 40 years ago!
A lot of stainless steel work was also carried out, as we polished every single rigging and deck item, even some of the rods, to a mirror finish just to please our eyes and for durability reasons. Now it is easier to see any cracks and maintain their good looks. We also finally had cleverly designed and integral bow ladders at the pushpit, so moving between the shore and the boat is much simpler now than before. We usually park bow-to here in the Baltic Sea. A new heavy duty stainless cradle for the 12” chart plotter at the helm was also manufactured by a very skilled friend of mine. As was the case with the bow ladders.
The teak decking had been replaced some years ago with the gluing method and it was still in good shape. During the late spring evenings, the co-skipper Karolina changed her suit for overalls, took a very sharp chisel and begun to shave the Sikaflex stripes back to the deck level. After that was finished, we finally sanding the deck with different power tools varying from a belt sander to a sanding mouse. To my surprise, I finally burned out my old and trustworthy belt sander during the last hours of the sanding job. We only got some sore knees, no other losses.
After we finally managed to put everything back in their places in the yacht it was time to start our summer cruise in the Baltic Sea. Of course with our two Siamese cats and even some miles with our daughters, but that’s another story.
During the next winters, the same show continued. Almost all the older systems were renewed as we prefer sailing during the summers, not repairing the boat. I’ve gained already enough experience of the latter one. The forepeak ceiling was refurbished, and a waste tank for the toilet was fitted there under the starboard bunk. All the inner lightning was replaced with new LED lights. A/C was installed under the starboard bunk in the after cabin and one branch of its ducting was led very carefully through the wardrobe to the main cabin. It really was a tight fit, but after all, a successful one! The engine gauges were replaced with new VDO OceanLine models and their wiring and mounting plates were restored and painted. Every item and system around the boat kitchen were also renewed. A high-pressure deck washing pump is supplying the fresh water system now and we can use it also for washing the anchor and chain. A cockpit shower with warm water was also installed.
We refurbished the Dorade vents with flexible car bumper paint, installed some new electronic devices, like an SSB receiver, Meteoman, Weather fax, and a new bigger warm water boiler with better insulation. The rest of the winches were replaced with self-tailing ones. Some new bilge pumps were fitted with high quality floating switches (Waterwitch). The original hydraulic backstay adjuster was leaking a bit and I bought a new Selden one to replace it. A new boom and cover were installed as we liked the idea of single rope reefing and the easiness of use of the zip-pack type boom cover. Well, we reef very seldom in the shelter of our archipelago. The remaining ropes were replaced by Dyneema ones and all the blocks are now Harken or Lewmar ball bearing ones from their Big Boat series. Our Kevlar main was torn to pieces in a blow just before the 50th Swan regatta, but after some phone calls, we found a solution. I ordered a new triradial Dyneema main during the autumn months from North Sails Finland sail loft. Some patches are also sewn to the DL Genoa 2 as the deck posts had punctuated it in two places. Those electrical Lewmar 54s for genoa sheets are almost too powerful when sheeting-in in a hurry!
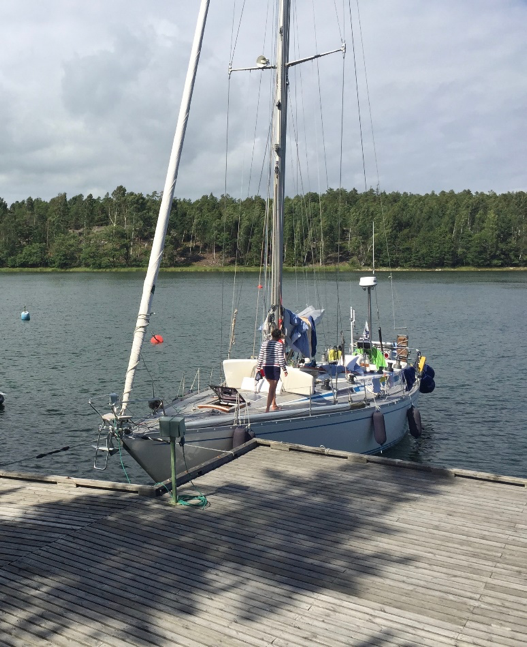
Maintenance break at island Svinö (TPS Yacht Clubs harbour)
Before the next launch we installed a Schenker 60 Digital Watermaker. It also helped us to double the fuel capacity as one of the three freshwater tanks was converted to a spare diesel tank. The watermaker is producing up to 60 liters of fresh water per hour, so we’ll be fine with just two tanks. One strictly for the spare water and one for the usage. I’ve already got all the parts needed for these tasks but must find the time and decent weather for the assembly. Remember, it’s snowing outside while I’m writing this!
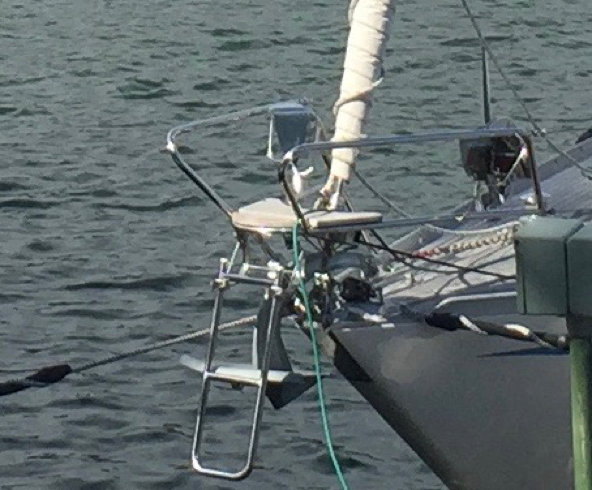
The clever design of the bow ladders, when sailing they fold away as seen in the first picture.
The engine room ventilation fan was to be replaced as the old one became too noisy and its ducting looks so battered as if it had been found from a scrapyard. It is probably original. New prisms are for the bridge deck were installed. The UV-radiation from the sun was enough to make the old ones brittle after only 8 years of use. I have to clean the surface rust from the mast supporting steel frame and paint it with industrial quality zinc-paint.
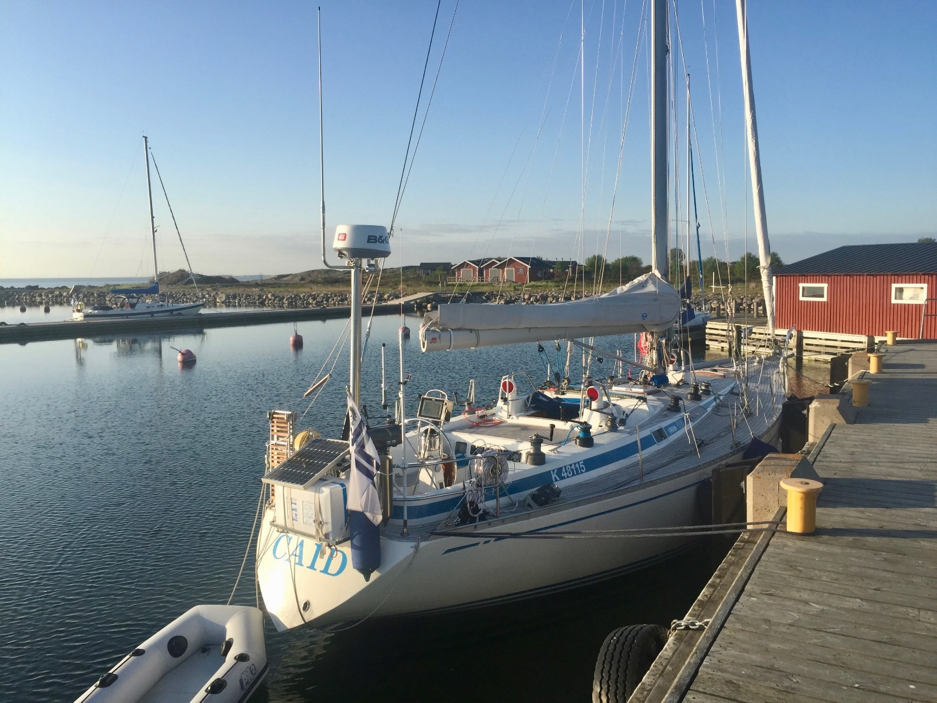
Early spring at Jurmo island, at the outer archipelago in Finland.
There are two old transducers on the bottom which should finally be removed and the holes laminated. I’ll be using the West epoxy for that job and hoping the final topcoat layer bonds to it as tested and claimed in ” Boatworks today” YouTube videos. We’ll see. A smallish bathing platform with integrated ladders was installed to the transom as we find it a bit difficult to climb back to the boat after swimming. I’m afraid we will be hearing some purist comments about ruining those classical S&S lines with this solution. After all, in trying to keep these old beauties sailing year after year, some concessions might have to be made!
2017-2019
During the long and cold winter in 2017, I somehow got very interested in using LiFePo4 batteries instead of the deep-cycle lead ones we already had. My main target was to at least double the usable capacity while using the same space reserved for the batteries. As usual, this project wasn’t a piece of cake like I first thought it’d be. The internet and especially YouTube are full of stories of this conversion very amateurishly done with some obviously worrying properties. Dunning-Kruger effect?
We also had some side projects going on as I ordered and installed a new Beta 50 diesel engine and a new Reckmann furler for the genoa using the old one for the staysail. But installing them did not require much effort. Good nerves were needed as the transport company somehow lost the track of our engine and it was lost for a while during the transport in spring. As usual these days, some of the specially ordered features to the engine were inadequately done and had to be rethought and redone.
There are some very clever LFP solutions available today which are already implemented and consist of every single item needed as the Victron or Mastervolt LFP systems. I just found them a bit pricey costing a way over 10k€ altogether for my intended use. After some very serious studying during autumn 2017, I installed our first LFP setup of my own design in spring 2018. It was a quite simple one as I followed the good old KISS method designing it for its intended testing purposes. A lot of parameters were entered to the different programmable power sources to have them behaving properly in this new lithium environment. I was very happy with my previous choice of the Victron charger/inverter as it was very easily adapted to this new system with some simple programming. I sold all the previous alternator related controllers etc and bought the only fully programmable one, a Balmar MC-614-H to be used with the Balmar alternator. So, this was a test setup for finding out if the technology is mature enough for our use. If this would not be the case, we’d easily continue with the existing lead acid ones. After using it for the summer of 2018 we found it very suitable and it was time to move on and design a more sophisticated setup.
After some serious thinking, I decided to rip off all the old battery cabling, fuses, switches etc and replaced them with new more beefier ones suited to this setup. For example, I will use only HD motorized switches and latching relays in the charging and discharging circuits controlled by the fully programmable BMS and also manually with the new battery control panel. Below are the pictures of the new battery control panel and some stage of the of the test setup project at home.
So has it been worth it so far? Economically – I think we all know the answer. But emotionally it’s a definitive YES as it’s a real pleasure to have a classic Yacht with sailing abilities above the ordinary and at the same time all the comforts of a new one.
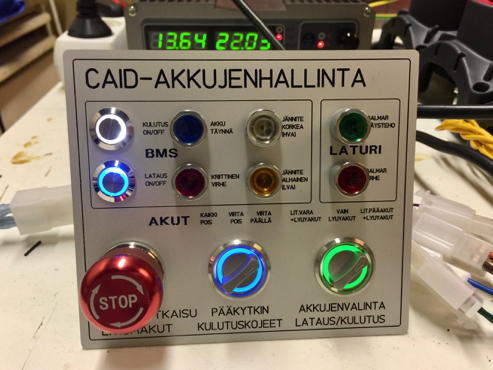
New battery management panel was specially made for CAID according to my CAD drawings.
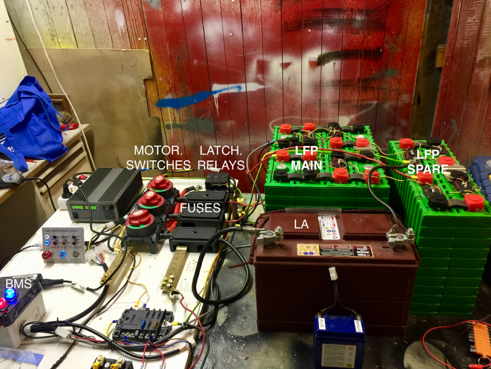
The latest stage of the LFP testing project at my home lab.
Great cruising season to all you S&S lovers,
Ilmari & Karolina Hentunen from Finland
Prezi, restoration (In Finnish)